Introduction to PPR Pipe
Polypropylene Random Copolymer (PPR) pipes have gained immense popularity in plumbing and construction due to their versatility, durability, and resistance to corrosion. These pipes are particularly known for their ability to withstand high temperatures and pressures, making them ideal for hot and cold water applications. The latest innovation in this field is the multilayer PPR Pipe reinforced with fiberglass, enhancing their performance and expanding their applications.
What Are Multilayer PPR Pipe?
Multilayer PPR pipes are composite pipes that consist of multiple layers of materials, typically combining PPR with other materials such as fiberglass or aluminum. This layering provides several advantages over traditional PPR pipes:
- Increased Strength: The fiberglass reinforcement significantly enhances the tensile strength and durability of the pipes.
- Reduced Thermal Expansion: Fiberglass helps minimize the thermal expansion of the pipes, maintaining their structural integrity under varying temperatures.
- Improved Insulation: The multilayer structure offers better thermal insulation, reducing heat loss in hot water applications.
Advantages of Fiberglass-Reinforced PPR Pipe
1. Enhanced Durability
Fiberglass-reinforced PPR pipes are designed to withstand harsh environmental conditions. The fiberglass layer protects the PPR from impact and reduces the likelihood of cracking or bursting, especially in extreme temperatures.
2. Lightweight and Easy to Handle
Compared to traditional metal pipes, PPR pipes are significantly lighter, making them easier to transport and install. The multilayer design maintains this lightweight characteristic while adding strength.
3. Resistance to Chemical Corrosion
PPR pipes are inherently resistant to many chemicals, and the fiberglass reinforcement further enhances this property. This makes them suitable for a wide range of industrial applications where chemical exposure is a concern.
4. Cost-Effectiveness
While the initial investment in fiberglass-reinforced PPR pipes may be higher than standard PPR pipes, the long-term savings in maintenance and replacement costs make them a cost-effective choice. Their durability ensures a longer lifespan, reducing the frequency of replacements.
5. Flexibility in Design
The multilayer nature of these pipes allows for greater flexibility in design and application. They can be manufactured in various sizes and shapes to meet specific project requirements, making them a versatile option for engineers and designers.
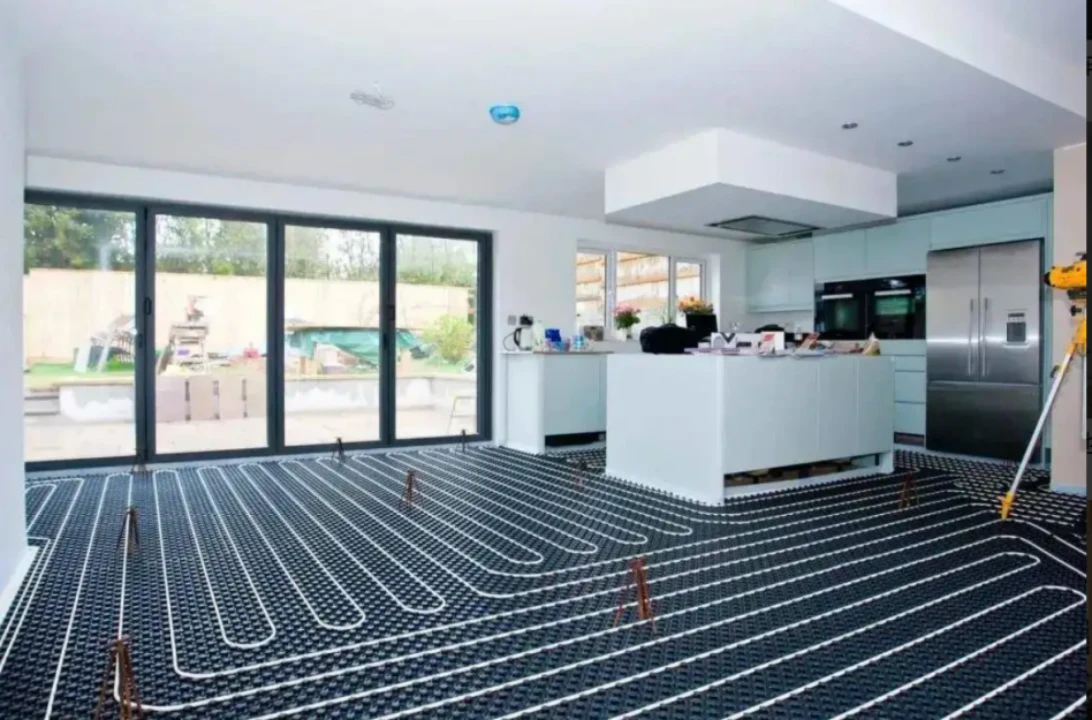
Applications of Multilayer PPR Pipe
The versatility of multilayer PPR pipes with fiberglass makes them suitable for various applications:
1. Residential Plumbing
In residential settings, these pipes are ideal for both hot and cold water supply systems. Their thermal insulation properties help maintain water temperature, enhancing energy efficiency.
2. Industrial Use
Industries that deal with corrosive chemicals benefit from using fiberglass-reinforced PPR pipes. They can handle high-pressure systems and are resistant to the chemical breakdown that can occur with other materials.
3. Heating Systems
The enhanced thermal stability of these pipes makes them perfect for heating systems, including underfloor heating and radiator connections. Their ability to withstand high temperatures without deforming is a significant advantage.
4. Agricultural Applications
In agriculture, multilayer PPR pipes can be used for irrigation systems. Their resistance to chemicals and weather elements ensures a reliable and long-lasting solution for farmers.
Installation Considerations PPR Pipe
1. Proper Tools and Techniques
Installing multilayer PPR pipes requires specific tools, including fusion welding equipment for joining the pipes. It’s essential to follow the manufacturer’s guidelines to ensure proper installation.
2. Expansion Considerations
Although fiberglass reinforcement reduces thermal expansion, it’s still important to consider expansion joints in long runs of piping to accommodate any potential movement.
3. System Design
Careful planning of the plumbing or piping system is crucial. Engineers should account for the pressure ratings and temperature limits of the specific multilayer PPR pipes being used.
Maintenance and Care PPR Pipe
One of the key advantages of PPR pipes is their low maintenance requirements. However, regular inspections are recommended to identify any potential issues early. Look for signs of wear or damage, especially at joint connections.
Environmental Impact
PPR pipes, including the multilayer variants, are generally considered eco-friendly. They are recyclable and have a lower carbon footprint compared to metal pipes. Furthermore, their durability means fewer replacements, contributing to less waste over time.
Conclusion PPR Pipe
The new generation of multilayer PPR pipes with fiberglass reinforcement represents a significant advancement in plumbing technology. Their enhanced durability, chemical resistance, and cost-effectiveness make them an ideal choice for various applications, from residential plumbing to industrial use. As demand for reliable and efficient piping solutions continues to grow, these innovative pipes are poised to play a crucial role in modern infrastructure.
FAQs
- What are PPR pipes used for? PPR pipes are commonly used for hot and cold water supply systems, industrial applications, and heating systems due to their durability and chemical resistance.
- How do fiberglass-reinforced PPR pipes differ from standard PPR pipes? Fiberglass-reinforced PPR pipes have an additional layer of fiberglass, providing increased strength, reduced thermal expansion, and improved insulation properties.
- Can multilayer PPR pipes be recycled? Yes, PPR pipes are recyclable, making them an environmentally friendly option compared to traditional materials.
- What temperature range can multilayer PPR pipes withstand? Multilayer PPR pipes can typically withstand temperatures up to 95°C (203°F) depending on the specific product and application.
- Are there specific installation requirements for multilayer PPR pipes? Yes, installation requires specific tools such as fusion welding equipment, and it’s essential to follow manufacturer guidelines for proper connections and system design.