PPR (Polypropylene Random Copolymer) and HDPE (High-Density Polyethylene) pipes DIN 8077/8078 are both widely used in plumbing and industrial applications. However, they have distinct characteristics and are suited for different uses. Below is a comparison highlighting the main differences between PPR and HDPE pipes.
1. Material Composition
- PPR Pipe: Made from Polypropylene Random Copolymer, a thermoplastic polymer, PPR pipes are known for their rigidity, strength, and resistance to high temperatures. They are specifically designed for hot and cold water systems.
- HDPE Pipe: HDPE pipes are made from High-Density Polyethylene, a strong yet flexible thermoplastic. HDPE pipes are versatile and used in a variety of applications, including water supply, gas transport, and sewage systems.
2. Temperature Resistance
- PPR Pipe: PPR pipes can withstand temperatures as high as 95°C (203°F), making them ideal for both hot and cold water systems, as well as heating applications.
- HDPE Pipe: HDPE pipes have lower temperature tolerance, generally up to 50°C (122°F). They are best suited for cold water applications and cannot handle high temperatures as effectively as PPR pipes.
3. Pressure Resistance
- PPR Pipe: PPR pipes have excellent pressure resistance, particularly in high-temperature environments. This makes them suitable for high-pressure applications in plumbing and heating systems.
- HDPE Pipe: HDPE pipes can also handle high pressure, particularly HDPE pipes with thicker walls. However, their pressure resistance decreases with temperature, limiting their use in high-temperature applications compared to PPR.
4. Flexibility
- PPR Pipe: PPR pipes are relatively rigid and lack the flexibility needed in certain applications, especially in areas with ground movement or where bending is required.
- HDPE Pipe: HDPE pipes are highly flexible and can bend easily without cracking, making them suitable for applications like trenchless installation, where flexibility is important. This flexibility allows HDPE to withstand ground movements, such as soil shifts or earthquakes.
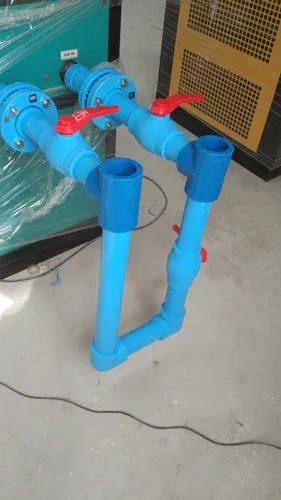
5. Chemical Resistance
- PPR Pipe: PPR pipes have good chemical resistance, particularly to acids, alkalis, and other chemicals used in water systems. They are commonly used in potable water systems due to their non-toxic nature.
- HDPE Pipe: HDPE pipes offer excellent chemical resistance to a wide range of chemicals, including strong acids, bases, and organic solvents. They are frequently used in industrial applications and chemical transport.
6. Installation
- PPR Pipe: PPR pipes are typically installed using heat fusion welding, creating strong, leak-proof joints. However, this process requires specialized tools and skilled labor.
- HDPE Pipe: HDPE pipes can also be joined using butt fusion, electrofusion, or mechanical fittings. They are easier to install in longer runs because of their flexibility, and they require fewer fittings, reducing potential weak points in the system.
7. UV Resistance
- PPR Pipe: PPR pipes have limited resistance to UV rays, and prolonged exposure to sunlight can cause them to degrade. Therefore, they are usually used indoors or need protective insulation if installed outdoors.
- HDPE Pipe: HDPE pipes, particularly black HDPE, are UV resistant and can be used in outdoor applications without degradation. This makes them ideal for irrigation systems and outdoor water supply lines.
8. Lifespan and Durability
- PPR Pipe: PPR pipes are highly durable and have a lifespan of over 50 years, particularly in controlled environments like indoor plumbing. They resist corrosion, scaling, and sediment buildup, ensuring long-term reliability.
- HDPE Pipe: HDPE pipes are also highly durable and have a similar lifespan of over 50 years. Their flexibility and resistance to environmental stress cracking make them ideal for outdoor use and systems subjected to ground shifts.
9. Cost
- PPR Pipe: PPR pipes tend to be more expensive than HDPE pipes, especially in hot water applications due to their higher temperature resistance. However, they offer long-term value in hot water and pressure systems.
- HDPE Pipe: HDPE pipes are generally more cost-effective, especially for large-scale projects like irrigation, water distribution, or sewage systems. Their flexibility also reduces installation costs in many cases.
10. Applications
- PPR Pipe:
- Hot and cold water supply systems
- Heating systems, such as underfloor heating
- Industrial piping for high-temperature fluids
- Potable water systems in residential and commercial buildings
- HDPE Pipe:
- Water distribution, especially for cold water
- Gas supply systems
- Sewage and drainage systems
- Irrigation systems
- Industrial fluid and chemical transport
- Outdoor piping exposed to sunlight or underground installations
Conclusion
PPR and HDPE pipes each have distinct advantages depending on the application. PPR pipes are the preferred choice for high-temperature and high-pressure systems, particularly for hot water and heating systems. They are also safe for potable water and are commonly used indoors. HDPE pipes, on the other hand, are flexible, resistant to UV and chemicals, and are ideal for outdoor, cold water, gas supply, and industrial applications. The choice between PPR and HDPE depends largely on the specific requirements of the project, including temperature, pressure, chemical exposure, and installation environment.