Introduction
A PPR (Polypropylene Random Copolymer) pipe NBR 15884 extrusion line is a specialized production setup designed to manufacture PPR pipes through the extrusion process. This technology allows for the continuous production of pipes with precise dimensions and properties, making it a popular choice in the plumbing and construction industries. This article provides an overview of the components, processes, and advantages of a PPR pipe extrusion line.
Key Components of a PPR Pipe Extrusion Line
- Extruder
- The heart of the extrusion line, the extruder is responsible for melting and homogenizing the PPR granules. It consists a screw mechanism that conveys the material through a heated barrel, where it melted and mixed before being pushed through the die.
- Die Head
- The die head shapes the molten PPR material into the desired pipe diameter and wall thickness. The design of the die is crucial for achieving uniformity and consistency in the final product.
Calibration Sleeve
- After the pipe exits the die, it passes through a calibration sleeve, which cools and shapes it to the required dimensions. This component ensures that the pipe maintains its shape and diameter as it solidifies.
- Cooling System
- A cooling system, often consisting a water bath or air-cooling setup, used to rapidly cool the extruded pipe. This helps to solidify the material and prevent deformation.
- Pulling System
- The pulling system, usually comprising caterpillar-type belts or rollers, moves the cooled pipe along the production line at a consistent speed. It ensures uniform tension and prevents sagging or deformation.
- Cutting Unit
- Once the pipe has been pulled to the desired length, a cutting unit slices it into predefined lengths. This unit can be automated to enhance efficiency and precision.
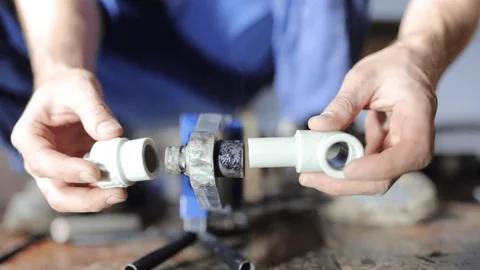
Control System
- An integrated control system manages the entire extrusion process, allowing operators to monitor temperature, pressure, and speed parameters. Advanced systems may also incorporate automation features for improved production efficiency.
The PPR Pipe Extrusion Process
- Material Preparation
- PPR granules are fed into the hopper of the extruder. The material often pre-dried to remove any moisture that could affect the extrusion process.
Melting and Mixing
- As the screw rotates within the extruder barrel, the PPR granules heated and melted. The mixing process ensures uniform consistency and eliminates any unmelted particles.
- Extrusion
- The molten PPR forced through the die head, forming a continuous pipe. The diameter and wall thickness determined by the design the die.
- Calibration and Cooling
- The extruded pipe then calibrated and cooled using the calibration sleeve and cooling system. This step solidifies the pipe and maintains its dimensions.
Pulling and Cutting
- The cooled pipe pulled along the line by the pulling system. Once it reaches the desired length, the cutting unit slices the pipe into individual pieces.
- Quality Control
- Finished pipes quality control checks to ensure they meet industry standards regarding dimensions, weight, and overall quality.
Advantages of PPR Pipe Extrusion Lines
- High Production Efficiency
- PPR pipe extrusion lines can operate continuously, allowing for high output rates. This makes them suitable for large-scale manufacturing.
- Consistent Quality
- The controlled extrusion process ensures uniformity in pipe dimensions and properties, resulting in high-quality products that meet industry standards.
Versatility
- Extrusion lines produce pipes of various sizes and thicknesses, catering to diverse market needs.
- Cost-Effective
- The efficiency of the extrusion process reduces production costs and waste, making it a cost-effective solution for manufacturers.
- Automation Potential
- Modern extrusion lines reducing labor costs and minimizing human error during production.
Conclusion
A PPR pipe extrusion line is an essential setup for manufacturers looking to produce high-quality PPR pipes efficiently. With its key components and streamlined processes, this technology enables the mass production of durable and reliable piping solutions for various applications in plumbing, construction, and beyond. As demand for PPR pipes continues to grow, investing in an advanced extrusion line can significantly enhance a manufacturer’s competitiveness in the market.