What are PPR Pipes?
Composition and Properties
PPR Pipe are made from a specific type of polypropylene that enhances their strength and durability. They are resistant to corrosion, scaling, and UV degradation, making them ideal for transporting hot and cold liquids.
Applications of PPR Pipes
PPR pipes are commonly utilized in residential and commercial plumbing systems, irrigation, and industrial applications. Their lightweight nature and ease of installation make them a preferred choice for many contractors.
Overview of the Production Process
Key Stages in PPR Pipe Manufacturing
The production of PPR pipes involves several stages, including:
- Compounding: Mixing raw materials to form a homogeneous blend.
- Extrusion: Shaping the melted polymer into pipe form.
- Cooling: Solidifying the extruded pipe.
- Cutting and Packaging: Finalizing the pipe into usable lengths.
Machinery and Equipment Used
Key machinery includes extruders, cooling tanks, and cutting machines. The efficiency and precision of these machines play a critical role in the final quality of the pipes produced.
Common Technical Problems in PPR Pipe Production
Material Quality Issues
Impurities in Raw Materials
One major technical problem in PPR pipe production is the presence of impurities in raw materials. Contaminated materials can lead to inconsistent pipe quality, affecting their performance and durability.
Inconsistent Polymer Grades
Variability in polymer grades can result in differences in physical properties, leading to issues like weak points in the pipes. This inconsistency can arise from supplier issues or improper storage conditions.
Production Process Challenges
Temperature Control Issues
Maintaining the correct temperature during the extrusion process is vital. Deviations can cause problems such as uneven melting of the polymer, resulting in defects in the final product.
Extrusion Problems
Extrusion is a critical stage where many issues can arise. Problems such as inconsistent pressure, screw wear, or material blockage can lead to poor-quality pipes or production downtime.
Causes of Technical Problems
Raw Material Sourcing
Supplier Reliability
The reliability of suppliers can significantly impact raw material quality. Inconsistent deliveries or poor-quality materials can lead to production delays and defects in the final product.
Quality Control in Raw Materials
Lack of rigorous quality control measures can allow subpar materials to enter the production process, exacerbating issues related to impurities and inconsistencies.
Machinery Limitations
Equipment Calibration
Improper calibration of machinery can lead to inaccuracies in the production process, causing defects in the pipes. Regular maintenance and calibration are essential for optimal performance.
Maintenance Issues
A lack of regular maintenance can result in machine breakdowns or inefficiencies, leading to production delays and increased costs.
Impact of Technical Problems on Production
Decreased Efficiency
Technical problems often lead to decreased production efficiency, resulting in longer lead times and increased costs. This inefficiency can hinder a manufacturer’s ability to meet demand.
Increased Waste
Production issues can result in higher waste levels, both in terms of materials and time. Excessive scrap can inflate costs and reduce profit margins.
Quality Compromise
When technical problems are not addressed, the quality of PPR pipes can suffer, leading to products that do not meet industry standards. This can result in product recalls or damage to the manufacturer’s reputation.
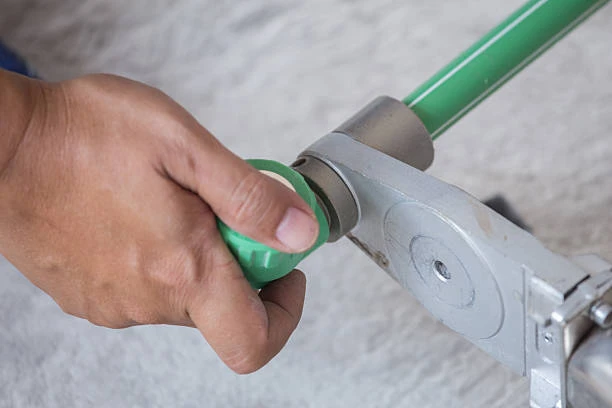
Solutions to Technical Problems
Improving Raw Material Quality
Implementing stricter quality control measures and working with reliable suppliers can significantly improve the quality of raw materials used in production.
Enhancing Production Processes
Advanced Machinery
Investing in modern, high-quality machinery can help mitigate many of the production issues associated with PPR pipes. Upgraded technology can lead to more precise control over the manufacturing process.
Staff Training
Providing adequate training for staff on operating machinery and recognizing potential issues can enhance overall production quality and efficiency.
Future Trends in PPR Pipe Production
Automation and Technology
The future of PPR pipe production will likely see increased automation, leading to greater efficiency and reduced error rates. Smart technologies will play a key role in monitoring production processes.
Sustainable Practices
As environmental concerns grow, manufacturers are likely to adopt more sustainable practices, focusing on reducing waste and improving the recyclability of PPR pipes.
Conclusion
Technical problems in the production of PPR Pipe can significantly impact efficiency and quality. By understanding the root causes of these issues and implementing effective solutions, manufacturers can enhance their production processes and deliver high-quality products.
FAQs
What is the average lifespan of PPR pipes?
PPR pipes typically have a lifespan of over 50 years when installed correctly, making them a durable choice for various applications.
How do I choose the right PPR pipe for my project?
Consider factors such as application requirements, pressure ratings, and local regulations when selecting PPR pipes for your project.
Are there specific certifications for PPR pipes?
Yes, PPR pipes often need to meet specific industry standards and certifications to ensure quality and safety.
What are the common applications for PPR pipes?
PPR pipes are widely used in plumbing, irrigation, and industrial applications due to their durability and resistance to corrosion.
How can I ensure the quality of PPR pipes?
Work with reputable suppliers, conduct regular quality control checks, and ensure proper installation practices to maintain pipe quality.