Introduction PPR Pipe
Polypropylene Random Copolymer (PPR) pipes have gained widespread acceptance in the construction industry due to their unique properties, including durability, resistance to corrosion, and versatility. However, despite their many advantages, quality problems can still arise during installation and use. This article will explore the common quality issues associated with PPR Pipe and provide practical strategies to prevent these problems, ensuring reliable and efficient performance in construction projects.
Understanding PPR Pipe
What are PPR Pipe?
PPR pipes are manufactured from a specific type of polypropylene known as random copolymer. This material provides PPR pipes with exceptional physical and chemical properties, making them suitable for a wide range of applications, including plumbing, irrigation, and industrial processes.
Advantages of PPR Pipe
- Durability: PPR pipes are known for their long lifespan, often exceeding 50 years under proper conditions. Their robust structure makes them resistant to wear and tear.
- Chemical Resistance: These pipes can handle a variety of chemicals, making them ideal for both residential and industrial applications. They are particularly effective in transporting corrosive fluids.
- Temperature Tolerance: PPR pipes can handle temperatures ranging from -40°C to +95°C, making them suitable for hot and cold water applications.
- Cost-Effectiveness: While the initial investment may be higher than other materials, the long-term savings from reduced maintenance and replacement costs make PPR pipes a cost-effective choice.
- Lightweight: PPR pipes are significantly lighter than metal alternatives, making transportation and installation easier and more efficient.
Common Quality Problems in PPR Pipe
Despite their advantages, several common quality problems can occur with PPR pipes. Understanding these issues and how to prevent them is crucial for ensuring the longevity and effectiveness of piping systems.
1. Deformation PPR Pipe
Deformation can occur due to improper handling, excessive heat, or pressure during transportation or installation. This can lead to misalignment and subsequent leaks.
Prevention Tips:
- Proper Handling: Ensure that PPR pipes are handled with care during transportation. Use appropriate equipment to avoid dropping or impacting the pipes.
- Temperature Control: Store pipes in a shaded, temperature-controlled environment. Exposure to direct sunlight or extreme temperatures can weaken the material and cause deformation.
2. Poor Joint Quality
The integrity of PPR piping systems relies heavily on the quality of joints. Weak joints can lead to leaks and eventual system failures, often arising from improper fusion techniques during installation.
Prevention Tips:
- Training and Certification: Ensure that installation personnel are adequately trained in the correct fusion methods, such as butt fusion or electrofusion. Certification programs can provide the necessary knowledge and skills.
- Quality Control: Implement strict quality control measures during installation. Regularly inspect joints and fittings for signs of improper bonding.
3. Cracking
Cracks can develop in PPR pipes due to thermal stress, mechanical impact, or improper installation techniques. These cracks compromise the integrity of the pipe and can lead to leaks.
Prevention Tips:
- Stress Analysis: Conduct thorough stress analysis before installation to identify potential weak points in the piping system.
- Use of Expansion Joints: Incorporate expansion joints into the design to accommodate thermal expansion and contraction, reducing the risk of cracking.
4. Scale Formation
Scale build-up inside PPR pipes can reduce flow efficiency and lead to clogs, affecting the overall performance of the plumbing system.
Prevention Tips:
- Regular Maintenance: Establish a routine maintenance schedule that includes inspecting and cleaning pipes to remove any scale build-up.
- Water Quality Monitoring: Regularly test the water quality to identify factors contributing to scale formation, such as hardness and mineral content. Use water treatment solutions as necessary.
5. Poor Installation Practices
Improper installation techniques can lead to various quality issues, including misalignment, leaks, and reduced lifespan of the piping system.
Prevention Tips:
- Follow Manufacturer Guidelines: Always adhere to the manufacturer’s installation guidelines. These instructions are designed to ensure optimal performance and durability.
- Proper Tools and Equipment: Use the right tools for cutting, joining, and installing PPR pipes. Ensure that equipment is calibrated and in good working condition.
PPR Pipe Installation Best Practices
1. Detailed Planning
Effective installation begins with careful planning. Assess the project requirements, including pipe diameter, length, and the expected flow rate.
- Design Considerations: Ensure that the design incorporates all necessary components, such as fittings, valves, and expansion joints.
- Environmental Factors: Take into account environmental conditions that may affect the installation process, such as temperature and humidity.
2. Quality Materials
Using high-quality PPR pipes and fittings is essential for minimizing defects and ensuring long-lasting performance. Always source materials from reputable manufacturers.
- Verify Certifications: Check that materials meet industry standards and have appropriate certifications for safety and quality.
- Inspect Materials: Conduct a thorough inspection of all materials before installation to identify any visible defects or damage.
3. Skilled Labor
Investing in skilled labor is crucial for successful PPR pipe installation. Ensure that all personnel involved in the installation process are trained and experienced.
- Training Programs: Implement ongoing training programs to keep workers updated on the latest installation techniques and safety practices.
- Safety Protocols: Establish and enforce safety protocols to protect workers during the installation process.
4. Comprehensive Testing
Before commissioning the PPR piping system, conduct thorough testing to ensure its integrity and performance.
- Pressure Testing: Conduct hydrostatic pressure tests to verify that joints and connections can withstand the expected operating pressure without leaking.
- Leak Detection: Use advanced leak detection technologies, such as acoustic monitoring, to identify potential leaks in the system.
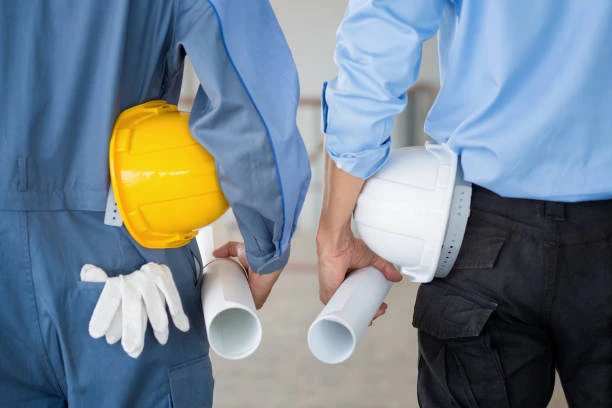
Regular Maintenance PPR Pipe
Importance of Maintenance
Regular maintenance is critical for the longevity and performance of PPR piping systems. A proactive maintenance schedule can prevent many common quality problems and ensure the system operates efficiently.
Maintenance Tips
- Visual Inspections: Regularly inspect visible sections of piping for signs of wear, damage, or leaks. Promptly address any issues to prevent further damage.
- Pressure Monitoring: Continuously monitor system pressure to detect any fluctuations that may indicate leaks or blockages.
- Cleaning Protocols: Implement cleaning protocols to remove debris, sediment, and scale build-up. Use appropriate cleaning agents and methods to avoid damaging the pipes.
- Documentation: Keep detailed records of maintenance activities, inspections, and repairs. This documentation can help identify patterns and inform future maintenance strategies.
Conclusion PPR Pipe
Preventing common quality problems in PPR pipes requires a proactive approach involving proper handling, installation, and maintenance practices. By following best practices and conducting regular inspections, stakeholders can ensure the reliability and longevity of PPR piping systems in construction projects. As the demand for efficient and sustainable plumbing solutions continues to grow, the proper management of PPR pipes will be crucial for successful infrastructure development.
Frequently Asked Questions (FAQs)
- What are the advantages of PPR pipes?
- PPR pipes are durable, resistant to corrosion, cost-effective, and can handle high temperatures, making them suitable for various applications.
- What common problems occur with PPR pipes?
- Common issues include deformation, poor joint quality, cracking, scale formation, and improper installation.
- How can I prevent leaks in PPR pipe joints?
- Ensure proper fusion techniques are used, and personnel are trained and certified in installation methods.
- What is the lifespan of PPR pipes?
- PPR pipes typically have a lifespan of over 50 years when properly installed and maintained.
- How often should PPR pipes be inspected?
- Regular inspections should be conducted at least annually, with more frequent checks for high-usage systems.