Chlorinated Polyvinyl Chloride, commonly known as CPVC, is a versatile thermoplastic widely used in various plumbing and piping applications. Its unique properties make it an excellent choice for both residential and commercial projects. This article will explore the manufacturing process of pipes, highlighting the significance of fittings and their applications in the industry.
Understanding CPVC and Its Advantages
CPVC is derived from PVC, with chlorine added during the polymerization process. This modification enhances its thermal stability and chemical resistance, making suitable for hot and cold water distribution systems. The primary advantages of CPVC include:
- High Temperature Resistance: CPVC can withstand temperatures up to 200°F (93°C), making it ideal for hot water applications.
- Corrosion Resistance: Unlike metal pipes, does not corrode, ensuring a longer lifespan.
- Lightweight and Easy to Install: CPVC is much lighter than traditional pipe materials, reducing installation time and labor costs.
- Cost-Effective: Compared to other materials like copper or steel, CPVC is generally more affordable, making it a popular choice among contractors and builders.
The Manufacturing Process of CPVC Pipes
The manufacturing of pipes involves several key steps, each crucial to ensuring the quality and performance of the final product.
1. Raw Material Preparation
The process begins with the procurement of high-quality PVC resin. This resin is mixed with chlorination agents, stabilizers, and other additives to enhance the properties of the resulting.
2. Chlorination
The prepared PVC resin undergoes a chlorination process. This involves exposing the resin to chlorine gas under controlled conditions. The degree of chlorination determines the quality and characteristics of the produced. Higher chlorination levels typically result in better thermal and chemical resistance.
3. Extrusion
Once the chlorination process is complete, the resin is fed into an extruder. The extruder heats the resin and forces it through a die to form long continuous pipes. The extrusion process is critical, as it shapes the pipes while maintaining uniform thickness.
4. Cooling and Sizing
After extrusion, the pipes are cooled using a water bath, which helps solidify their shape. Proper sizing ensures compatibility with fittings, which are essential for jointing and connecting different sections of the piping system.
5. Quality Control
Quality control is a vital aspect of pipe manufacturing. Each batch undergoes rigorous testing to ensure that it meets industry standards for strength, flexibility, and chemical resistance. This includes pressure testing and inspection for any defects or inconsistencies.
6. Packaging and Distribution
Once the pipes pass quality control, they are packaged for distribution. Manufacturers often bundle the pipes based on size and application, making it easy for contractors and retailers to access the products they need.
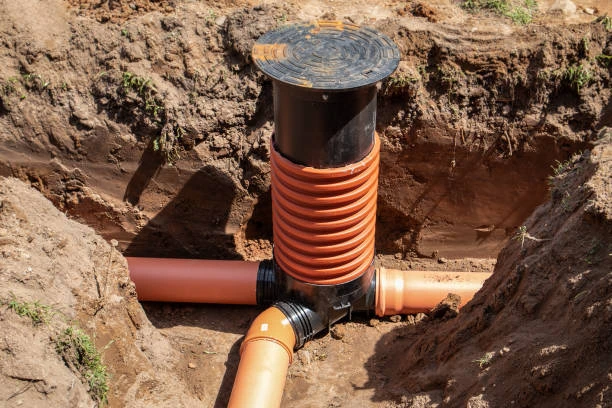
The Role of CPVC Fittings
CPVC fittings are integral components in any plumbing system. These fittings connect various pipe sections, allowing for changes in direction, branching, and transitions between different pipe sizes. Common types of fittings include:
- Elbows: Used to change the direction of the piping system, typically at 90 or 45 degrees.
- Tees: Allow for branching off in multiple directions, essential for creating complex plumbing layouts.
- Couplings: Connect two sections of pipe together, providing a secure and leak-free joint.
- Adapters: Facilitate connections between pipes and other materials, such as copper or PVC.
The quality of fittings is equally important as the pipes themselves. High-quality fittings ensure reliable connections, preventing leaks and maintaining the integrity of the entire plumbing system.
Applications of CPVC Pipes and Fittings
CPVC pipes and fittings are widely used across various applications, including:
- Residential Plumbing: Ideal for both hot and cold water supply lines, offering a reliable solution for homeowners.
- Commercial Buildings: Used in commercial plumbing systems due to their durability and resistance to corrosion.
- Industrial Applications: CPVC’s chemical resistance makes it suitable for transporting aggressive fluids in industrial settings.
- Fire Sprinkler Systems: CPVC pipes are often used in fire protection systems, as they can handle high temperatures and pressures.
Conclusion
CPVC pipe manufacturing is a complex but rewarding process that results in a highly durable and versatile product. As the demand for high-quality plumbing solutions continues to grow, CPVC pipes and fittings stand out as a leading choice for contractors and builders across various industries.
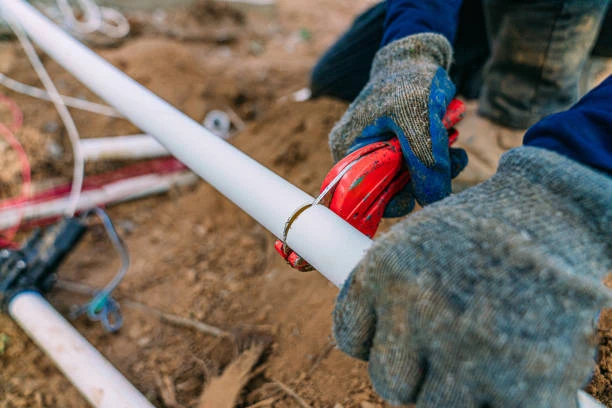
Frequently Asked Questions (FAQs)
1. What are CPVC fittings?
CPVC fittings are connectors used in plumbing systems made from chlorinated polyvinyl chloride, designed to join different sections of pipes.
2. How do CPVC pipes compare to PVC pipes?
CPVC pipes can withstand higher temperatures than PVC pipes, making them suitable for hot water applications.
3. Are CPVC fittings easy to install?
Yes, fittings are lightweight and can be easily glued together, making installation straightforward for professionals and DIY enthusiasts alike.
4. Can CPVC pipes be used for outdoor applications?
While is resistant to UV light, it is generally recommended for indoor use. If used outdoors, proper protection should be provided to prevent degradation.
5. What is the lifespan of CPVC pipes?
CPVC pipes have a long lifespan, often exceeding 50 years when properly installed and maintained.